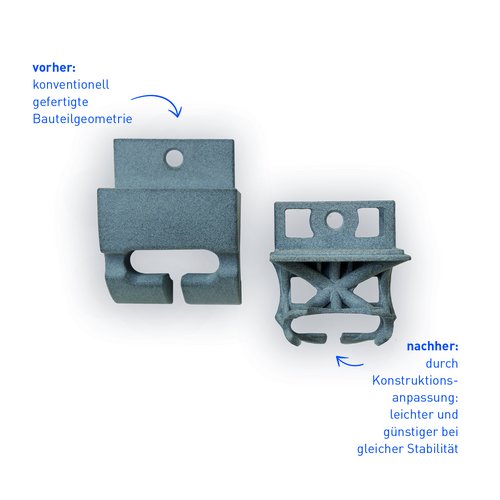
Next Generation: Additive Manufacturing
Anyone familiar with product design understands the challenge of constantly optimizing individual components, and thus also of reducing costs. In some projects this is easily achieved, in others, not so much. But what if this were always possible – regardless of the component and its geometry? If you think outside the box somewhat and are open to new ideas, that’s exactly what additive manufacturing offers.
But for which industries are 3D plastic and rubber (polymer) components best suited? In principle, they can be used in any sector: heavy industry, medical technology, capital goods, plastics and rubber, and even furniture manufacturing. Additive manufacturing has become increasingly important in recent years. This is because, compared to conventional process technologies, this technology offers a simple way of producing components with intricate, complex structures and shapes quickly, cost-effectively and sustainably.
One of Germany’s most innovative companies in the field of additive manufacturing is the SPÄH Group based in Scheer. In addition to the material polyamide 12 (PA12), SPÄH also offers a special combination of MJF technology and polypropylene (PP). In collaboration with SPÄH, several well-known companies are already exploiting the characteristic features of additive manufacturing by designing their individual components as a single casting – with no limits in terms of the geometry.
Therefore, the reputation of additive technology as only being suitable for prototypes has been wide of the mark for some time now. Currently, depending on the component, quantities of 20,000 up to 50,000 pieces per year are perfectly feasible. The dynamic production process means that design changes can be implemented without great effort – even during series production. With 3D printing, there are no setup and tooling costs, which is a major advantage. And compared to conventional manufacturing processes, the material properties are also absolutely comparable. Depending on the desired material, the individual products are weather-resistant as well as UV-resistant, sturdy and impact-resistant.
This process technology offers additional added value by allowing design adaptations. In its customer projects, SPÄH has achieved material savings of up to 50% and component weight reductions of up to 60% through design-related optimizations and material changes – with improved functionality and unchanged rigidity. These adjustments made the respective components 30–50% more cost-efficient on average.
In addition, the pressure from companies to manufacture more sustainably is increasing. In order to reduce the carbon footprint in the long term, one option is to switch to additive manufacturing processes. As a production process, it already has some sustainable characteristics. For example, 100% of the surplus base material is mixed with virgin material and reused. Other aspects include regional procurement, shorter delivery times, short transport routes and reduced inventories (on-demand production).
Photo: Before-and-after comparison of a “fixture”, sector: automation